10 Common Mistakes That Cause Workplace Burn Injuries
Heat, electricity, chemicals, and radiation can cause significant burns, affecting employees in a wide range of industries. As we approach next week’s Burn Awareness Week, safety professionals can benefit from understanding many of the errors that lead to worksite burns.
January 28, 2025
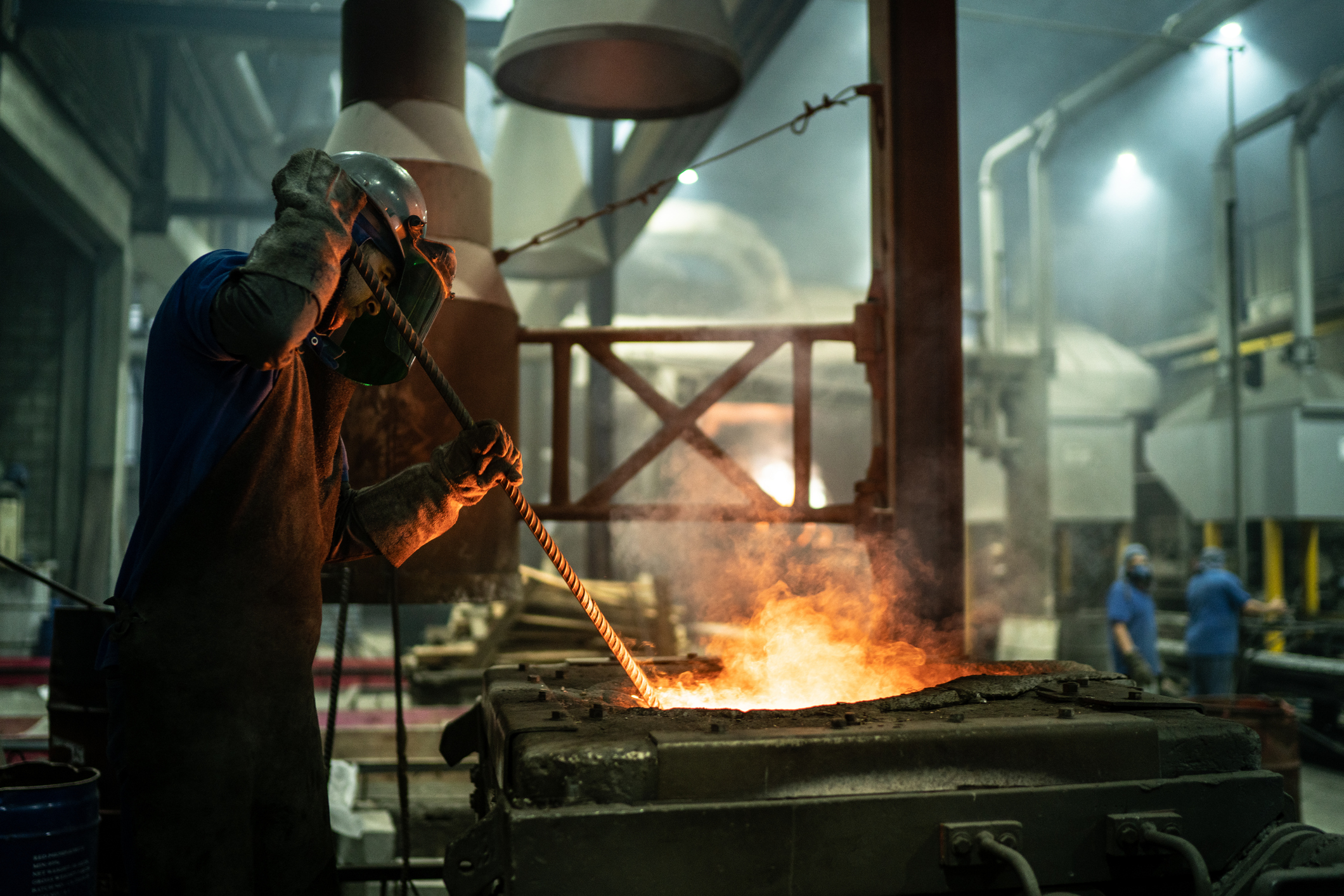
Burn injuries in the workplace can be particularly catastrophic due to their severity, pain, and recovery time. However, they are usually preventable with proper equipment maintenance, training, and handling.
“Burn injuries related to open flames or hot liquids are among some of the most well-known work hazards, but electrical and chemical burns must also be addressed,” said Kevin O’Sadnick, Senior Risk Control Manager at Safety National. “Adequate training and well-established safety programs are critical in preventing painful and costly burns.”
These are some of the most frequent errors that result in workplace burn injuries.
1. Mishandling coffee pots, hot water spigots for tea, cooking and open flame areas.
These commonly used items seem harmless, but the standard workplace coffee maker can reach brewing temperatures between 195 and 205 degrees. While these situations typically result in first-degree burns, a damaged coffee pot can malfunction, resulting in second-degree burns.
2. Misuse of corrosive chemicals, such as acids or alkalis.
These substances can cause chemical burns, often worse than heat burns, due to their ability to penetrate the skin and cause further tissue damage. These chemicals should always be used with protective gear in a well-ventilated area and be clearly labeled, stored, and disposed of properly.
3. Neglecting radiation exposures.
Medical technicians, lab researchers, air crews, construction workers, and industrial operations employees all face potential radiation exposure. X-rays, CT scanners, and radioactive isotopes have various uses in these industries and can result in radiation burns. Even exposure to ultraviolet rays can result in radiation burns, as sunburn is considered the most common type of radiation burn. Sunburn can be prevented through sunscreen, protective clothing, and limited sun exposure. More specific applications, like X-rays, require lead aprons and shielding barriers.
4. Inadequate training.
Proper training should cover handling hazardous materials, operating machinery, and following safety protocols. When burn exposures occur in the workplace, clear procedures should be developed for reporting burn incidents, administering appropriate first aid, and evacuating the area if necessary.
5. Poor equipment maintenance.
When regular hazard assessments are skipped or delayed, even the smallest undetected defect in machinery can cause a major injury. Regular inspection and maintenance can quickly identify if machinery is likely to overheat, malfunction, or potentially spill hot or hazardous materials.
6. Lack of warning signs or barriers.
Color codes, posters, labels, and signs to notify employees of potential hazards are vital for hazard communication and are extremely important to burn prevention. Safety data sheets (SDS) should be kept onsite and include handling instructions, accidental release measures, first aid, and fire-fighting measures.
7. Unattended spills or leaks of hot liquid.
Slips, trips, and falls are still the most common type of workplace injury, and when hot, hazardous liquids are added to the equation, a severe burn can also result. Equipping and training employees, paired with reinforcing housekeeping practices, can reduce premise hazards. It is recommended that someone remains at the site of a spill, monitoring and ensuring that it is cleaned up within minutes.
8. Failure to follow lockout/tagout (LOTO) procedures.
LOTO protocol prevents equipment from unexpectedly powering on or releasing stored energy. Often, hidden energy sources are present after the main energy source has been disconnected from the equipment. Controls to eliminate or reduce the risk of these energy sources are required to properly de-energize machinery. A policy that ensures proper de-energization can help eliminate arc flash exposures, especially during regular maintenance.
9. Misjudging situational awareness.
Working around dangerous materials that are in close proximity, like overhead power lines, requires maintaining appropriate safe distances. This includes being present, actively observing your surroundings, avoiding distractions and focusing on what is happening around you. On an active worksite, it can be the difference between a near miss and a fatality.
10. Lack of personal protective equipment (PPE).
Flame-resistant gloves, clothing, or face shields can prevent burn exposure. For those handling radiation-emitting materials or machinery, PPE may include leaded gloves, lead aprons, and thyroid shields. A fire watch should be utilized with an appropriate fire extinguisher nearby during hot work operations.