How to Improve Situational Awareness in Your Workforce
Can situational awareness be learned, developed, or enhanced? Routine practice of this skill can be key in modifying unsafe acts that lead to accidents in the workplace.
November 6, 2023
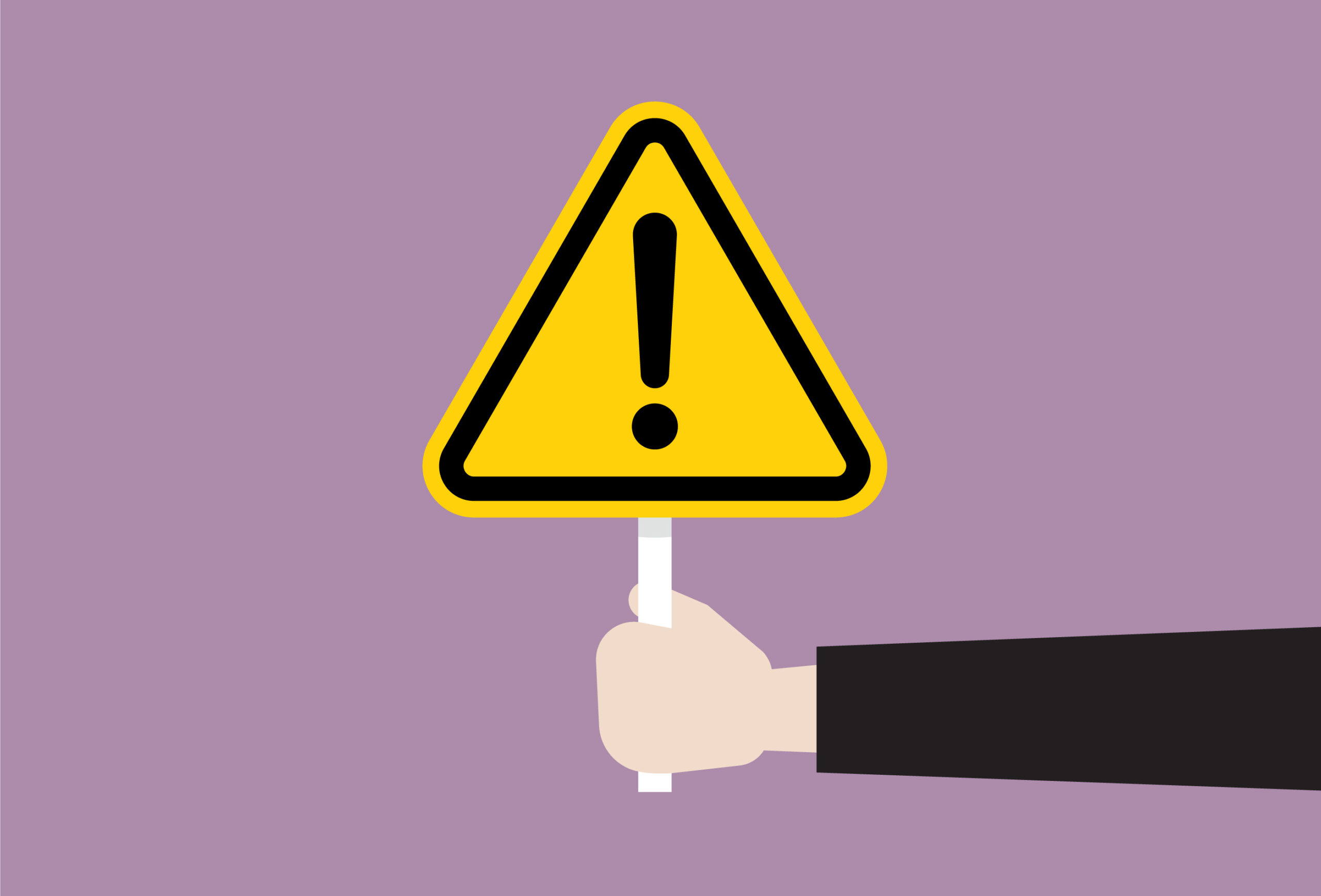
Situational awareness is the ability to perceive and understand the environment around you, including people, objects, events, and their potential impact on your goals and safety. It includes being present, actively observing your surroundings, avoiding distractions and focusing on what is happening around you. On an active worksite, it can be the difference between a near miss and a fatality.
“It may seem like a natural trait to individuals, but it is actually a skill that can be developed with practice and conscious effort,” said Ed Pratt, Director – Risk Services at Safety National. “However, employers should lead the charge through continual assessment of the workplace, alerting employees of any ongoing changes in a worksite. Complacency and comfort go hand in hand with a lack of situational awareness.”
Situational Awareness in Action
The process of situational awareness involves four steps: identifying relevant information, comprehending what it means, explaining how it affects the current situation, and acting accordingly.
- Identify: Have you ever heard the term “check your six?” More commonly, it refers to “watch your back,” and in regard to situational awareness, it is the first step in alerting an employee to immediate dangers. Do they know what objects or people are in their immediate area, particularly when handling hazardous materials or driving heavy machinery?
- Process: After identifying potential risks, employees should understand how these risks might affect their current tasks. For example, an employee notices a spill on a production line floor while driving a forklift. Have risk management leaders trained them in the principles of “if you see it, you own it”? Or will they drive over it, leaving a larger trail for others to slip on?
- Comprehend: An employee has processed the potential risk at hand, but can they comprehend what it means to overall risks? Do they understand that if they do not immediately clean up a spill, it could lead to someone else’s serious injury?
- Act: What happens after they comprehend the danger and its implications? Action is the critical last step in breaking the chain of continuous risk. In the event that the risk is not something they can attend to or remediate, do they know who to contact for support?
How Employees Can Improve Situational Awareness
A common statement from any accident report might sound like this: “I never saw the other vehicle,” “I had no idea he was standing there,” or “I did not know there was a step there.” Any statement that begins like this might have been avoided through the practice of situational awareness. Improving this skillset starts with encouraging employees to:
- Use all their senses: Engage the senses when gathering information about the work environment. This includes not just using visual cues but also what they hear, smell, and feel.
- Anticipate and predict: Develop the ability to anticipate and predict potential outcomes based on the information they gather. This helps stay prepared and make better decisions.
- Stay informed: Stay updated on current events, trends, and developments that may affect the work environment. This includes being aware of local news, weather conditions, and relevant information about their surroundings.
- Avoid fatigue: Employees scheduled for long hours will naturally be tired, and exhaustion is likely to lead to mistakes or injuries. Injuries can be prevented by ensuring that employees are not working double shifts and are scheduled appropriately to allow for breaks.
- Reflect and debrief: After any situation, employers should take the time to reflect on what happened and evaluate their employee’s level of situational awareness. Identify areas for improvement and learn from experiences, knowing where training opportunities might have made a difference.
For more expertise, guidance or resources on this topic, please contact [email protected].