Product Safety: A Critical Responsibility for Companies
Defective design, poor manufacturing, and non-compliance with regulations are liability exposures that can put a business at risk for producing an unsafe product. Adopting strict safety measures can minimize these risks, preventing injuries, property damage, or fatalities in the process.
May 3, 2025
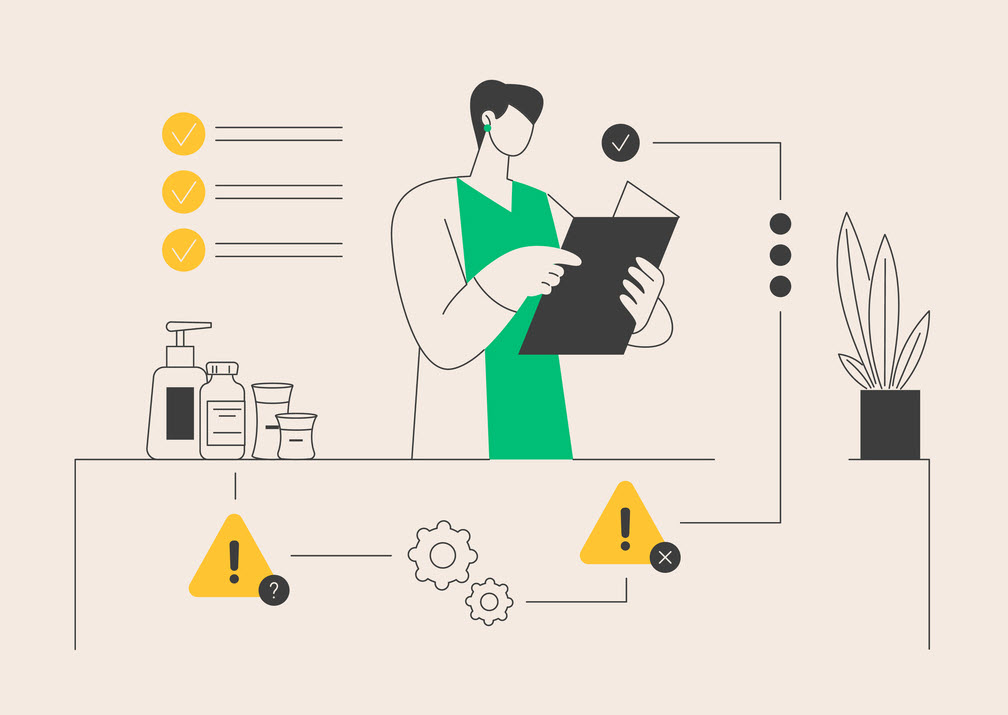
Product safety is a fundamental responsibility for companies across all industries. Whether manufacturing consumer goods, electronics, food, or industrial equipment, ensuring that products are safe for use protects both customers and businesses.
“A company’s brand credibility and consumer trust rely on safety prioritization,” said Vik Ramaswamy, Risk Control Director – National Liability and Complex Risk Leader at Safety National. “Poor product safety can also result in lawsuits, recalls, and financial losses. Following safety regulations, conducting rigorous testing, labeling properly, and ensuring supply chain accountability may help protect consumers and an organization’s brand reputation.”
By adopting strict product safety measures, companies can protect consumers, minimize liability risks, and maintain compliance with legal standards. Here are several best practices that may help ensure product safety.
1. Follow Regulatory Standards
Every industry has specific safety regulations and guidelines that companies must follow to protect consumers against unreasonable risks of injury. Two of the governing bodies that set these standards include:
- Consumer Product Safety Commission (CPSC) regulations in the U.S.
- International Organization for Standardization (ISO) safety certifications.
Ensuring compliance with these safety standards helps prevent recalls and legal actions.
2. Implement Rigorous Testing and Quality Control
Pre-market testing can help to identify potential hazards before a product reaches consumers. Organizations may benefit from using third-party testing and certification for unbiased quality assurance. Performing random batch inspections may catch manufacturing defects, but manufacturers should also monitor real-world product performance and update designs if necessary.
3. Ensure Clear Labeling and Instructions
Appropriate labeling is key to preventing misuse and identifying potential hazards. Labels may include:
- Detailed usage instructions
- Clear safety warnings
- Internationally recognized symbols for cautionary labels
- Multilingual instructions, especially Spanish wherein U.S. markets
4. Monitor Supply Chain Safety
Organizations should only work with reliable and certified suppliers who can ensure that product components will meet safety standards and regulations. Businesses should conduct regular audits of these manufacturers and suppliers to detect any safety concerns. Additionally, ethical sourcing has become increasingly important to avoid toxic substances and unsafe labor practices.
5. Train Employees on Product Safety Protocols
Developing an internal safety culture that encourages employees to uphold important standards requires thorough training. Employees should be educated on quality control processes, risk assessments, identifying defects, and reporting safety concerns.
6. Establish a Recall and Incident Response Plan
Manufacturers should have a rapid recall system in place to address defective products efficiently. Maintaining a customer complaint tracking system can also help identify recurring safety issues. In the event of a recall, all product issues should be communicated openly with consumers and regulatory agencies.
7. Stay Proactive with Consumer Feedback and Updates
Collecting and analyzing customer feedback may detect emerging safety concerns. Advances in technology and materials can drastically improve products, but considering consumer experiences can also be key in updating product designs and instructions.