Streamlining and Simplifying the Prosthetic Approval Process
Lack of specialized knowledge can make workers’ compensation claims that include prosthetic assessment and approval extremely challenging and costly. Here are three steps to include in the process that, through collaboration, can help direct these claims to the best possible outcomes.
May 5, 2022
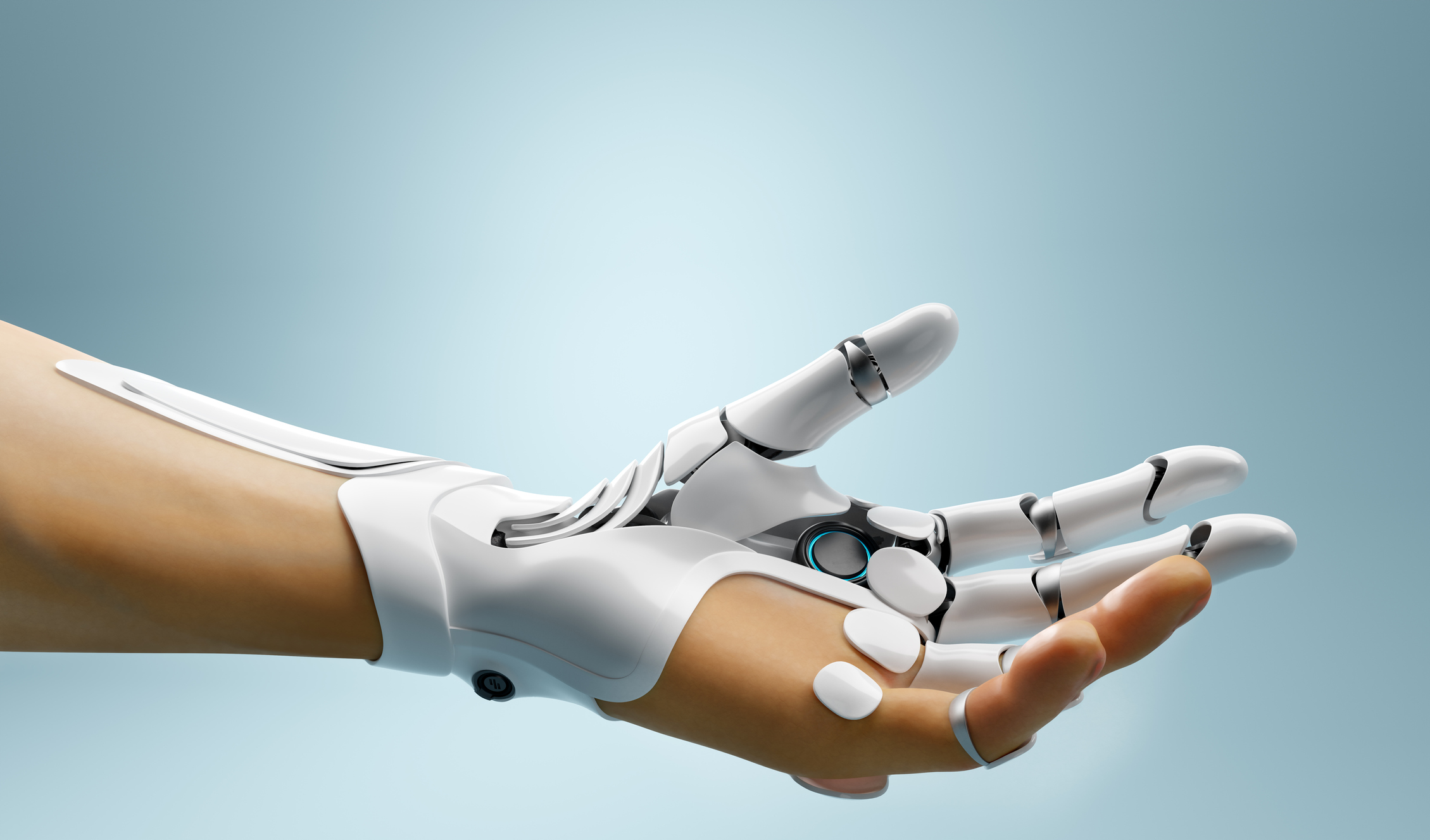
When an injured worker requires a prosthetic, claims managers must balance several complicated factors. First, accurately matching the prosthetic to the patient’s lifestyle and ability to operate is critically important. Failure to do so can lead to significant exposure potential – especially since the need for a replacement can occur every four-to-seven years. In addition, evaluating the multitude of costs associated with the process is not common knowledge and can require special expertise to manage properly. The right approach, however, can help steer this extremely complex process to the best possible outcomes for all involved.
“A claim that includes prosthetics is a long-term and expensive commitment for all stakeholders, including the patient, TPA and excess workers’ compensation carrier,” said Stacy Whalen, Senior Medical Manager at Safety National. “Understanding how to navigate the prosthetics process can not only maximize the injured worker’s overall functional recovery, but also mitigate inflated, duplicative and unnecessary costly expenditures that can rapidly lead to exceeding an organization’s self-insured retention level.”
Here are some important steps for claims managers to consider when evaluating and approving prosthetic orders.
1. Making the Match
It is imperative to match the right prosthetic to each individual. Make sure the prosthetic fits the injured worker’s lifestyle and functional needs. Prosthetics range from purely cosmetic with minimal function to highly adaptive myoelectric units offering various joint and digit mobility levels. The cost variation in prosthetics is significant depending on the body part, number of joints involved and technology. For example, some very effective basic limbs may cost $20,000, but a highly specialized hand and fingers unit can cost as much as $180,000. It is easy to see where getting the right unit to the right person is so important. These are not “throw-away” pieces of equipment.
When a prosthetician is assessing the injured worker, make sure their report accurately reflects the age, weight, job function, ability to operate and activity lifestyle of the patient.
2. Conducting Due Diligence
Prosthetics are a significant investment, therefore it is reasonable to pursue the most accurate and competitive pricing. Obtaining more than one quote is strongly recommended. It is common to see multiple pages of various codes making up the total cost. The codes will include individual costs for sockets, microprocessors, sleeves, joints and other items that go into “building” a prosthetic. Have someone familiar with the codes assess each line item of the quote. Making sense of this information can be daunting, but scrutinizing the codes for accuracy and potential duplication is an important step in cost control.
This is where adjusters should tap into their resources. Contacting your excess carrier is a great place to start. Often the carrier has deep relationships with medical service providers that can review those pages of codes and costs in detail. Again, the goal is to determine if you are getting the best prosthetic match for the individual at the right cost.
These expert vendors can help analyze the various quotes and explain them to you, providing assistance to confirm prosthetic pricing and appropriateness before approval is issued. The review process does not take long for the vendors that specialize in this area of expertise. In fact, they typically want to help. You just have to ask.
3. Avoiding Expensive Mistakes
As mentioned, prosthetics can range from around $15,000 – $200,000 depending on the unit, so devoting time to the process and adjusting treatment when necessary is important. Remember, this limb will most likely have to be replaced every four-to-seven years, or possibly sooner if the injured worker has complications with the residual limb. One often-overlooked factor is the complicated learning curve for an amputee. For example, with a prosthetic leg, the patient must learn to balance, walk, and ultimately care for the prosthetic for the long term. The more complex the unit, the more lengthy the learning curve. When we fail to match the injured worker with a prosthetic that is functional and easy for them to use, the individual often quits wearing it, wasting the time and monetary investment that went into the process.
It is also important to understand how other factors like weight gain and skin integrity can come into play. Since the socket is vacuum fitted to each individual, weight fluctuation and skin breakdown prohibits a proper fit. Further to that, the hardware necessary to make that adjustment occasionally becomes discontinued, and an entire new prosthetic must be provided as a replacement.
Lack of education and attentiveness during the assessment and approval process can lead to potentially avoidable cost drivers, which can quickly add up over a lifetime.